New battery recycling techniques set to transform environmental impact of electric vehicles
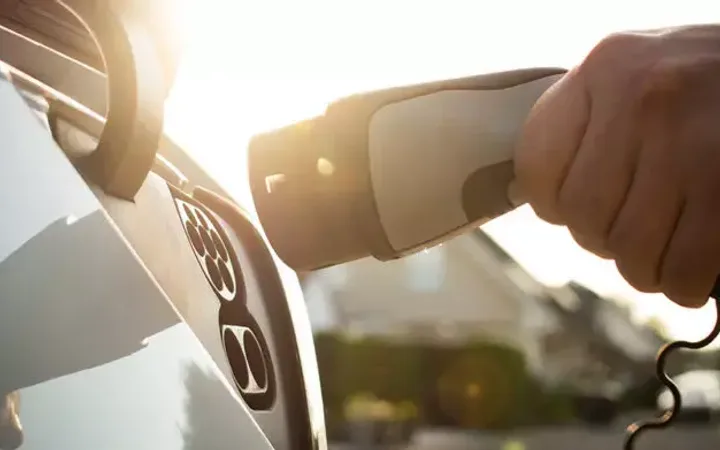
As the world transitions away from using fossil fuels for energy generation, heating and transportation, the need for large-scale energy storage increases — and with this comes mounting economic and environmental concerns around the end-of-life management and processing of batteries. Here, we explore recent research into new and chemical-free recycling methods that can extend the usability of battery components and help us build towards a more sustainable future.
Rapid market growth and battery ageing
With the global market for grid-scale storage — required to smooth the inevitable peaks and troughs in supply from renewable wind and solar installations — forecast to increase six-fold between 2020 and 2026, alongside analyst predictions of impressive growth rates for the automotive battery market in the next decade — with battery electric vehicles predicted to make up over 80% of new vehicle sales by 2030 — the environmental and social impacts of raw material mining (particularly lithium and cobalt) for batteries is worrying.
Ageing restricts the usable lifetime of batteries through capacity loss and increased resistance. While electric vehicle manufacturers seek to mitigate the effects of battery ageing through oversizing and sophisticated battery management systems (which optimise charge levels and rates), eventually all EVs and energy storage systems will reach the end of their usable lives and the resulting waste will need to be processed.
Recycling the components of spent batteries will help to reduce the reliance on virgin materials and the subsequent environmental damage.
Material extraction techniques
Most existing commercial scale recycling methods focus on the extraction of valuable elements (such as Co, Ni, Li, Mn) from the battery. Batteries are dismantled and spent cathodes and anodes are shred into a powder. This powder is then processed either by pyrometallurgy[i] (which is very energy intense and leads to loss of materials) or hydrometallurgy[ii] (which requires harsh chemicals and produces toxic waste gas and water).
Recent research has focused on trying to reduce the environmental impact of pyrometallurgical and hydrometallurgical processes. A recently published patent application from researchers at Nanchang University[iii] reports a low temperature pyrometallugical process using composite salts to selectively extract lithium from spent cathodes. A further application from The University of Science and Technology Beijing[iv] relates to the use of a bifunctional oxalic acid-based eutectic solvent which acts both as leaching and reducing agent.
There have also been some studies into the use of bacteria to selectively digest and reduce metal oxides to metal nanoparticles.[v]
Direct recovery without chemicals
Given the complexity and environmental costs associated with extracting valuable elements from spent batteries, some researchers are increasingly looking at methods of recovering and regenerating useful components without chemical methods.
One of the challenges associated with the direct recovery and reconditioning of battery components is the disassembly of complex battery systems. There is no standardisation in battery pack design and manual disassembly is time consuming, complex and hazardous. The Faraday Institution’s ReLiB project is working on automated systems for battery disassembly and has developed an ultrasonic delamination method to separate metal foils from the active material surface which is much faster than conventional acid-based methods.[vi]
Once separated, spent mixed metal oxide cathode materials can be regenerated by adding a fresh source of lithium (usually Li2CO3), calcination and then reforming the electrode. Studies have also shown that by treating cells with supercritical CO2, lowering temperature and pressure, and then separating CO2 from the electrolyte, the electrolyte can be regenerated.[vii] Research into the direct recycling of battery components has mainly focused on the cathode and electrolyte, as the value in recovering a graphite anode is lower. However, anode recovery is also possible.[viii]
Commercialisation and IP protection
The benefits of recycling battery components will become more acute as increasing numbers of EV and other batteries reach end of life. Existing recycling processes will be improved to be industrially applicable and new technologies will be developed to deal with both established and emerging battery materials.
With patents able to protect both new processes and improvements to existing ones, we are likely to see a lot of IP activity, with innovators looking to steal a march on their competitors as the demand for battery components accelerates.
If you’re innovating in this space, get in touch with me for a free initial chat about protecting your technology.
Our chemistry and materials team will be exhibiting at the Advanced Materials Show at NEC, Birmingham (UK) on 29 and 30 June 2022. Come and see us in Hall 18 (stand 525) to find out how we work with innovators throughout the supply-chain, helping to secure valuable IP rights and build portfolios that protect and enhance their business.
[i] B. Makuza et al, Journal of Power Sources, 491, 2021, 229622
[ii] Y. Fan et al, ACS Sustainable Chem. Eng., 6, 2018, 13611-13627
[iii] CN113415814A
[iv] CN113871744A
[v] Mishra et al, Waste Manag., 2008, 28, 333-338
[vi] Abbott et al, Green Chem., 2021,23, 4710-4715
[vii] Yang et al, Green Chem., 2018, 20, 3121-3133
[viii] Sabisch et al, Resour. Conserv. Recycling, 2018, 129, 129-134